This article is Part 5 of the “How to See Waste: the 7+1 Muda – Office edition” on the Zerwaste blog. In this post, I will explore the sixth of the eight wastes of Lean: Inventory Excess
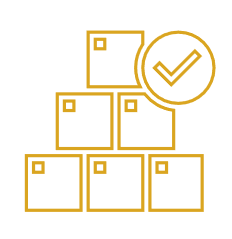
Welcome back to my Lean Six Sigma Journey! In the past weeks, I have introduced the concept of Lean and explored its origins in the manufacturing field building on Henry Ford’s innovative approach to revolutionizing production processes and Japan’s Taiichi Ohno with Toyota Production System (TPS).
So far, we have learned that Lean is a transmittable, transmutable concept that can be abstracted and applied to every aspect of a business regardless of industry, be it in education, healthcare, software development, consultancy, and so forth. We have also learned that the first step to Lean is to identify all value-adding and non-value-adding activities. Your next step is to eliminate the wasteful activities.
By doing so, Lean allows you to cut waste and maximize the efficiency of your resources by focusing on only value-adding activities. In the simplest terms, Lean helps you cut the fat from your processes so you can focus on what matters. However, your work does not stop there. Lean invites you to apply those principles permanently and everywhere in your organization. This is called continuous process improvement which paves the way to operational excellence.
This brings us to our “How to See Waste” Series – Lean Office edition. With it, we want to open your eyes and help you see the individual as well as universal types of waste in an office environment. By doing so, we hope both businesses and individuals understand the importance of Lean thinking and can apply those principles in the office and beyond.
In the first post of the series, I introduced the eight types of waste which are as follows:
- Defects
- Overproduction
- Waiting
- Non-utilized Talent
- Transportation
- Inventory Excess
- Motion Excess
- Extra-processing
Lean Office: How the Muda of Inventory Excess Looks Like in an Office
In a traditional business setting, Inventory Excess refers to the excess of any kind of office material such as computers, office equipment, furniture, stationery, papers, paperwork, and archives. Corporate offices for example are known for purchasing office supplies in copious quantities before they are needed to save money or to have them ready when new employees join.
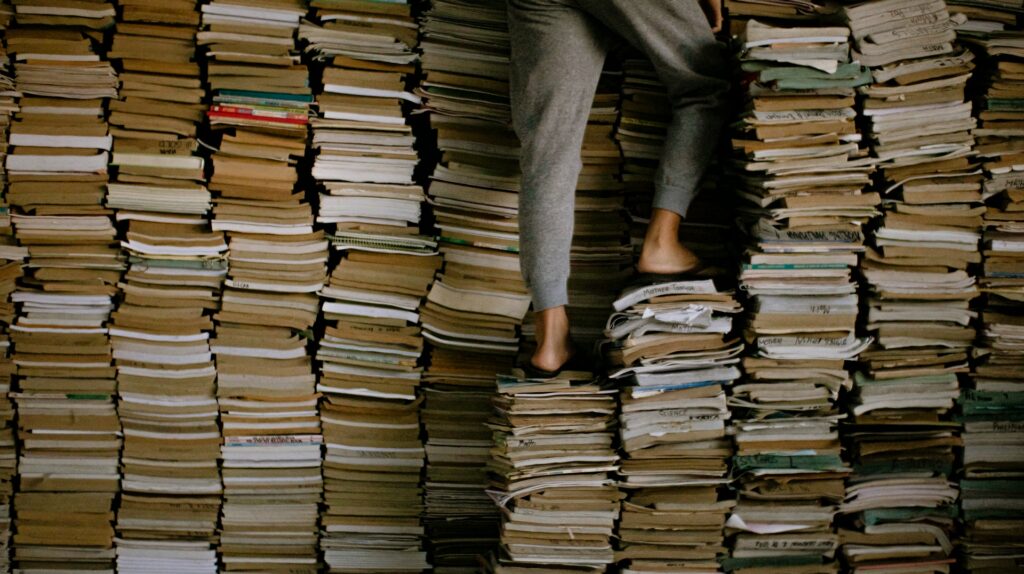
Nowadays, Inventory Excess is a term that encompasses any physical or digital product that is in a waiting phase. It refers to the accumulation of WIP (Work in Progress). It can be overloaded inboxes, unfinished tasks, long to-do lists, bottlenecks in the project development pipelines, and unbalanced resource assignment charts. If you want to be able to detect this form of waste, try to look at any resource in your workspace. If that resource is sitting idle and waiting to be utilized or processed, that means it is being wasted.
The Muda of Inventory Excess in the office can take (but is not limited to) any of the following forms:
- Unread email, full inboxes
- Excessive office supplies: parts, furniture, stationery, paperwork, archives
- Any form of batch processing: i.e., transactions, reports
- Obsolete files or office equipment
- Unfinished projects in the pipeline
- Purchased software that is not being deployed
How to Eliminate the Muda of Inventory Excess
To eliminate Inventory Excess in your office, start by identifying any physical and digital inventory and making lists of any resources that are not being used. Management of this inventory can be vital to keeping your customers satisfied and your employees productive.
When it comes to physical Inventory waste such as office supplies, start by auditing, organizing, and storing everything properly. Paper waste in offices remains one of the biggest forms of physical waste. Before starting any print job, ask yourself: do all processes require paper files? Can this be done digitally? When purchasing office supplies, do not order bigger batches than what you need to save money on bulk buying- This will hurt you eventually. Even when renting an office, extra space that is not being utilized is considered waste. Adhering to Just-In-Time (JIT) from Lean Principles when approaching any activity or resource can help significantly reduce this type of waste in the office.
When it comes to digital products or processes, inventory waste can be a sign of a deeper problem. It usually denotes unclear planning, uneven workloads, and poor cross-training. Do not overload your employees with multiple projects at the same time. And if you do, make sure you are assigning projects only when other projects are finished or passed from the employee department in question to another. Cross-training your employees is also important to avoid this kind of waste as it allows for more flexibility in managing projects during peak times or in case an employee is suddenly absent.
Finally, do not overpromise your customers. Always be transparent on delivery time and only commit to reasonable timelines. Applying lean principles to achieve clear planning, balanced workloads, and efficient processes will help target this type of waste as it reduces the amount of Work-In-Progress. Using Kanban Planning Tools such as Kanban boards will allow for even assignment of resources and therefore avoiding bottlenecks in your project development pipeline.