This article is Part 2 of the “How to See Waste: the 7+1 Muda – Office edition” on the Zerwaste blog. In this post, I will explore the first of the eight wastes of Lean: Defects.
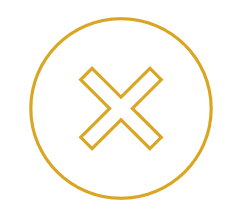
Welcome back to my Lean Six Sigma Journey! In the past weeks, I have introduced the concept of Lean and explored its origins in the manufacturing field building on Henry Ford’s innovative approach to revolutionize production processes and Japan’s Taiichi Ohno with his Toyota Production System (TPS).
So far, we have learned that Lean is a transmittable, transmutable concept that can be abstracted and applied to every aspect of a business regardless of industry, be it in education, healthcare, software development, consultancy, and so forth. We have also learned that the first step to Lean is to identify all value-adding and non-value-adding activities. Your next step is to eliminate the wasteful activities.
By doing so, Lean allows you to cut waste and maximize the efficiency of your resources by focusing on only value-adding activities. In the simplest terms, Lean helps you cut the fat from your processes so you can focus on what matters. However, your work doesn’t stop there. Lean invites you to apply those principles on a permanent basis and everywhere in your organization. This is called continuous process improvement which paves the way to operational excellence.
This brings us to our “How to See Waste” Series – Lean Office edition. With it, we want to open your eyes and help you see the individual as well as universal types of waste in an office environment. By doing so, we hope both businesses and individuals understand the importance of Lean thinking and are able to apply those principles in the office and beyond.
In my previous post, I introduced the 8 types of waste which are as follows:
- Defects
- Overproduction
- Waiting
- Non-utilized Talent
- Transportation
- Inventory Excess
- Motion Excess
- Extra-processing
Lean Office: How the Muda Defects Look Like in an Office
It is easy to think of different instances of defects in the manufacturing field. However, if we were to apply the same concept to identify defects in the office, the task will not be as simple. Defects in the office take a completely different form.
The Muda of defects is any work or activity that did not accomplish the desired result, contained incomplete/conflicting information, or did not meet client demands. It is work that you have completed but requires reworking. Anything that must be reworked, corrected, or clarified is considered a waste because it forces to use double the resources (time, money, availability) to complete the same task.
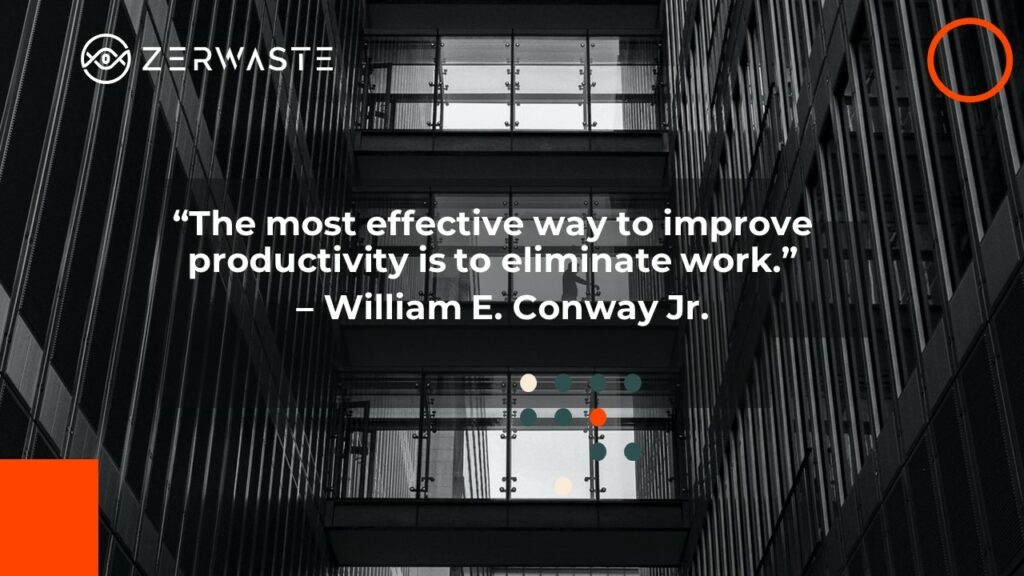
In the office, defects are often labeled as errors. Such errors would be missing order numbers in an excel sheet, typos in an advertising banner, a bug in your developer’s code, a missing attachment, a late report, etc… Such errors would require you to spend additional resources to correct, rectify and optimize the process. In lean manufacturing, Machines are responsible for the error while in the office it is more likely that the error is human made. However, it is important to know that even human processes can be improved and optimized to decrease the chances of errors happening in the same way.
Muda Defects in the office can take (but not limited to) any of the following forms :
- Incorrect information
- Conflicting information
- Insufficient information
- Partially complete work or information
- Missing attachment, file names, lost files, or information
- Late work
- Data entry errors
- Errors that run undetected
- Design flaws
- Manual keying generating errors
- Spreadsheet errors
- Invoice errors

How to Eliminate the Muda of Defects
An error that makes it through to your final product can result in a significant amount of waste. Errors as small as a typo in your print campaign or wrong calculations in a spreadsheet that made it into your stakeholders’ meeting can set you back significantly. These kinds of errors will not only decrease customer satisfaction. They will also require you to rework your campaign or your budget causing more waste.
Defects mean doing things wrong. They are the result of bad processes. That means once you fix the process, you eliminate defects and resulting waste. However, the real danger of the Muda of defects lies in its possibility to run undetected for a long time. This causes a snowball effect that increases proportionally to how long it takes for the defect to be identified: the further an error gets passed downstream, the bigger the waste. This is why it is important to identify these errors as early as possible.
Can human errors be avoided? The short answer is No. Human errors will always occur and Lean principles acknowledge that. For that, it invites you to this type of Muda by putting in place processes to proofread, fact-check, crosscheck or double-check any outbound material. By running final testing and quality assessment after each stage concludes in your process, you will ensure that your team detects errors when and where they occur. Other solutions could include automating, standardizing, and consolidating repeated work.
Moreover, Lean focuses on the ‘first-time right’ principle which aims to create processes that perform in the right manner from the first implementation. By developing the right processes from the start, you can guarantee higher productivity, efficiency, and success.
Product designer Paolo Cardini asks questions about our way of life and answers them with whimsical and playful examples. During his appearance in the TED Talks, he asks the question of the efficiency of multitasking and the possibility of being monotask. He uses an example of a barbecue. He presented an image of burnt meat as a result of different activities being done at the same time. He was able to do all the activities but one of them, which was the main one, had to be done again.