This article is Part 8 of the “How to See Waste: the 7+1 Muda – Office edition” on the Zerwaste blog. In this post, I will explore the seventh of the eight wastes of Lean: Motion Excess
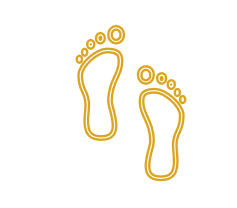
Welcome back to my Lean Six Sigma Journey! In the past weeks, I have introduced the concept of Lean and explored its origins in the manufacturing field building on Henry Ford’s innovative approach to revolutionizing production processes and Japan’s Taiichi Ohno with Toyota Production System (TPS).
So far, we have learned that Lean is a transmittable, transmutable concept that can be abstracted and applied to every aspect of a business regardless of industry, be it in education, healthcare, software development, consultancy, and so forth. We have also learned that the first step to Lean is to identify all value-adding and non-value-adding activities. Your next step is to eliminate the wasteful activities.
By doing so, Lean allows you to cut waste and maximize the efficiency of your resources by focusing on only value-adding activities. In the simplest terms, Lean helps you cut the fat from your processes so you can focus on what matters. However, your work does not stop there. Lean invites you to apply those principles permanently and everywhere in your organization. This is called continuous process improvement which paves the way to operational excellence.
This brings us to our “How to See Waste” Series – Lean Office edition. With it, we want to open your eyes and help you see the individual as well as universal types of waste in an office environment. By doing so, we hope both businesses and individuals understand the importance of Lean thinking and can apply those principles in the office and beyond.
In the first post of the series, I introduced the eight types of waste which are as follows:
- Defects
- Overproduction
- Waiting
- Non-utilized Talent
- Transportation
- Inventory Excess
- Motion Excess
- Extra-processing
Lean Office: How the Muda of Motion Excess Looks Like in an Office
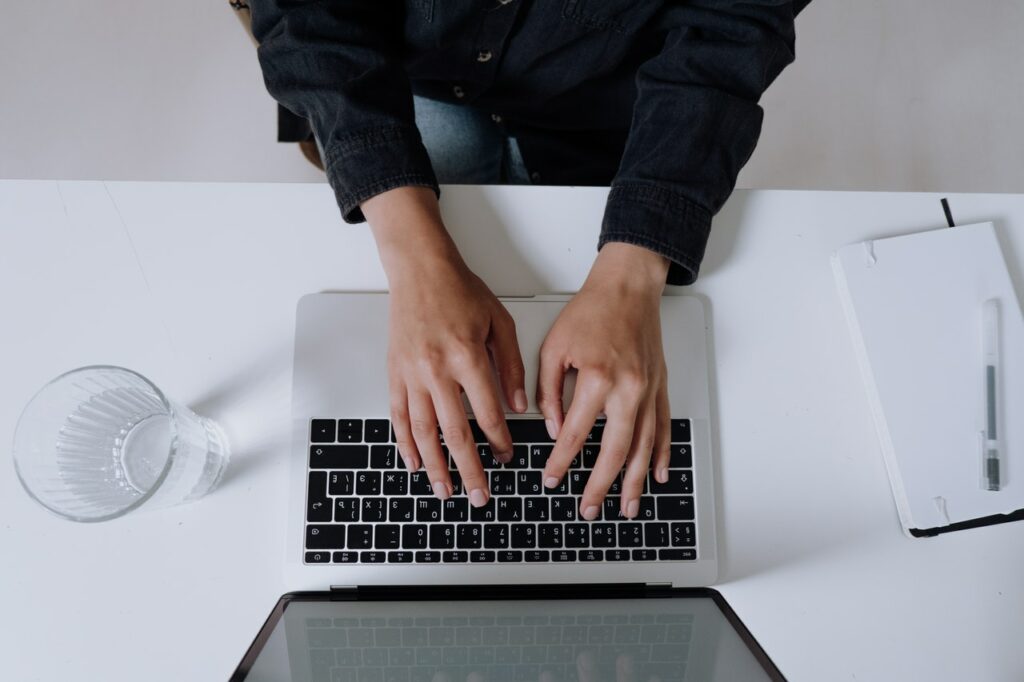
In a business setting, Motion Excess is any unnecessary or excessive motion that does not produce any value. In paper-based offices, it can be going back and forth to the copier, flipping through papers, etc. In a digital office, motion excess is any excessive movement that occurs when an employee is using their computer. Working with slow old computers, software that crashes often, and poorly-mapped file systems are all examples of time-consuming inefficient activities. Another way motion excess manifests itself in a modern office setting is attending meetings without being able to produce unless a decision is made, or new plans are developed during the meeting.
The Muda of Motion Excess in the office can take (but is not limited to) any of the following forms:
- Poor workstation/office layout
- Walking between offices
- Movement of people from and to meeting rooms
- Extra keystrokes
- Excess mouse clicks
- Scrolling up and down a computer screen
- Shuffling through paper
- Manual data entry
- Walking to/from photocopier/printer
- Employees not working to a standard method
- Searching for files on the computer
- Sorting through materials
- Poor process design
- Shared equipment and machines
- Siloed operations
How to Eliminate the Muda of Motion Excess
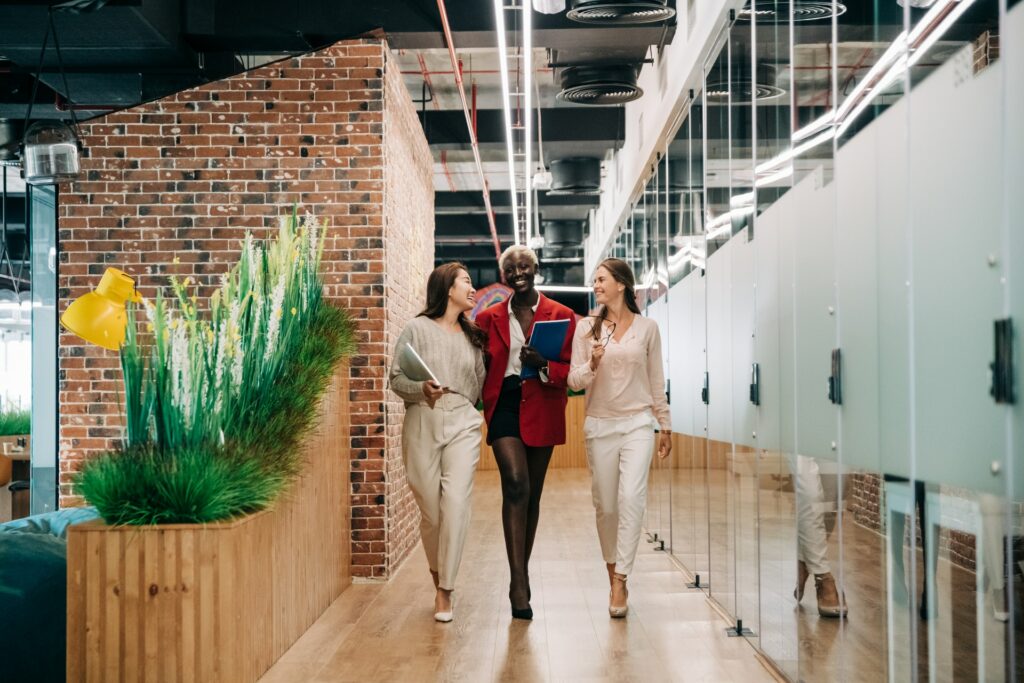
Any task that requires excessive motion is considered waste and therefore should be redesigned to improve the productivity of the employees while safeguarding their health, safety, and overall job satisfaction. In lean manufacturing, the way to deal with motion excess is to make each motion as small, efficient, and ergonomic as possible. However, the bigger question is: how can we eliminate motion excess from knowledge work?
To eliminate the Muda of Motion Excess from the office, start by asking yourself: Can we adjust the physical layout of the office to optimize productivity and ergonomics? To do so, check if teams who constantly work together are placed in proximity. Verify that office equipment is close to the people who use it most. A good office plan ensures that employees can access up to 90% of the resources they need by taking a direct path on the floor they work on. Making sure that the office space is designed with employee movement in mind can save you and your employees a lot of time. A well-organized office optimizes employee productivity and ergonomics and safeguards their time and health.
Moreover, there exist as mentioned above hundreds of wasted motions in a digital office– manually inputting data, chains of emails, searching, and filing. Employees should be able to complete their tasks and access needed data, files, websites, and software with little effort. A good lean method to manage this type of waste is to use document management systems, follow standardized processes, provide sufficient and relevant training to employees and deploy business process automation solutions.