This article is Part 5 of the “How to See Waste: the 7+1 Muda – Office edition” on the Zerwaste blog. In this post, I will explore the fifth of the eight wastes of Lean: Transportation Excess
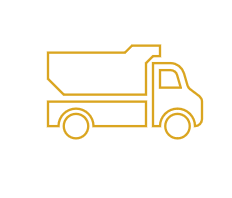
Welcome back to my Lean Six Sigma Journey! In the past weeks, I have introduced the concept of Lean and explored its origins in the manufacturing field building on Henry Ford’s innovative approach to revolutionizing production processes and Japan’s Taiichi Ohno with Toyota Production System (TPS).
So far, we have learned that Lean is a transmittable, transmutable concept that can be abstracted and applied to every aspect of a business regardless of industry, be it in education, healthcare, software development, consultancy, and so forth. We have also learned that the first step to Lean is to identify all value-adding and non-value-adding activities. Your next step is to eliminate the wasteful activities.
By doing so, Lean allows you to cut waste and maximize the efficiency of your resources by focusing on only value-adding activities. In the simplest terms, Lean helps you cut the fat from your processes so you can focus on what matters. However, your work does not stop there. Lean invites you to apply those principles permanently and everywhere in your organization. This is called continuous process improvement which paves the way to operational excellence.
This brings us to our “How to See Waste” Series – Lean Office edition. With it, we want to open your eyes and help you see the individual as well as universal types of waste in an office environment. By doing so, we hope both businesses and individuals understand the importance of Lean thinking and can apply those principles in the office and beyond.
In the first post of the series, I introduced the eight types of waste which are as follows:
- Defects
- Overproduction
- Waiting
- Non-utilized Talent
- Transportation Excess
- Inventory Excess
- Motion Excess
- Extra-processing
Lean Office: How the Muda of Transportation Looks Like in an Office
In the traditional office setting, Transportation Excess was used to represent the movement of information and people. Nowadays, with hyperconnected digital offices, most information is sent over email, shared through a cloud service, or uploaded company server. This means that transportation waste still occurs but occurs digitally making it more difficult to detect.
The Muda of transportation in the office is any unnecessary movement between stages of a process. This means when looking at the life cycle of a task, any movement from one state to the other is transportation. Let’s take a report approval for instance. A report is firstly written, then sent for proofreading, and then sent for approval before publishing. The movement of the report between each employee or stage represents a trip of the product. So, this means the more people included in the process of the editing, proofreading, and final approval the longer the report will be in transit. Transportation of electronic data is extremely sensitive because it often results in multiple, varying copies of the work, which must eventually be reconciled. It leads to other wastes such as defects, overproduction, and processing.
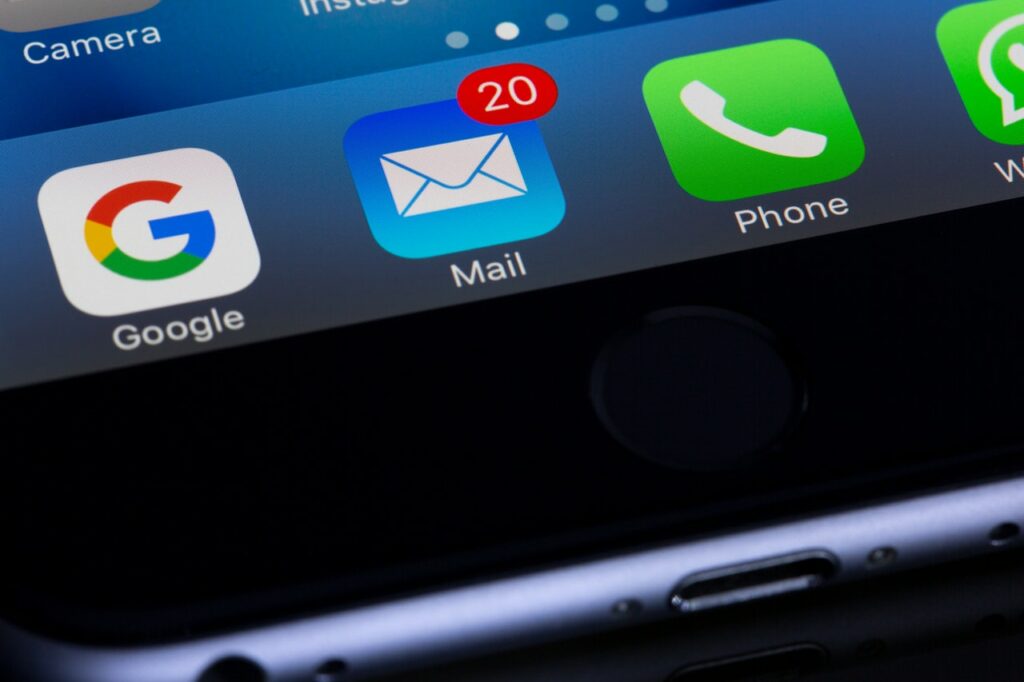
The main cause of transportation waste in the office is inefficiently designed processes. Like what happens on the factory floor, any process that requires extra movement or multiple storing/approval destinations is wasteful. This could be any task or document that is moving back and forth due to miscommunication, unclear requirements, or poor quality of execution. Transportation also creates more room for errors and defects when the work goes to the wrong person or fails to get to the right person.
The Muda of Transportation Excess in the office can take (but is not limited to) any of the following forms:
- Unnecessary movement of paperwork, boxes, equipment
- Moving products in and out of storage
- Going back and forth to meeting rooms
- Multiple handoffs of electronic data through the various departments
- Multiple approval levels
- Bad area/department layout
- Excessive filing of documents
- Excessive email attachments
- Distributing unnecessary cc copies to people who don’t need to be in the loop
How to Eliminate the Muda of Transportation
To eliminate the Muda of Transportation when carrying on a task, start by asking: Is this step necessary? Signing documents, reports, cc in emails – could any of these steps be made more efficient, eliminated, or even automated? If the act of transporting the item in question does not contribute to its advancement or add any value to it, then this means this step can be eliminated.
Transportation Excess in the office may not seem like an urgent problem to address. However, we are hoping by helping you gain a better understanding of how this type of waste can manifest itself in a business setting, you will be able to understand how it can affect the way you do business. One of the main concepts in Lean is continuous process improvement and understanding that a process doesn’t need to be broken in order to be revised. Lean invites you to revisit and examine each process, whether by human or machine, to optimize its efficiency and eliminate wasteful practices. Applying lean principles to eliminate Transportation Waste means starting with process design by creating flow between processes, defining clear roles, excessive meetings and not over-producing work-in-process (WIP) items.
Moreover, as the entire world has already made the shift to remote work, it has become more clear that the movement of employees from and the office to conduct tasks that they could normally carry out remotely is now seen and recognized as waste. What COVID has taught us that you are losing time when your employees are spending a considerable amount of time commuting while they could use this time to be productive. Knowing when your employees are needed in the office and planning their office hours around that will help you reduce transportation excess.
Finally, physical space must always be considered. One method to eliminate this waste is by reducing the distances items/people must travel. Offices must be designed with roles in mind: teams that require frequent face-to-face meetings or collaborations for instance should be assigned to the same office space. Proximity in this case reduces waste costs by transportation.