This article is Part 4 of the “How to See Waste: the 7+1 Muda – Office edition” on the Zerwaste blog. In this post, I will explore the third of the eight wastes of Lean: Waiting
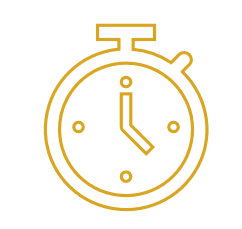
Welcome back to my Lean Six Sigma Journey! In the past weeks, I have introduced the concept of Lean and explored its origins in the manufacturing field building on Henry Ford’s innovative approach to revolutionizing production processes and Japan’s Taiichi Ohno with Toyota Production System (TPS). (“How To See Waste – Muda #1: Defects – Zerwaste”)
So far, we have learned that Lean is a transmittable, transmutable concept that can be abstracted and applied to every aspect of a business regardless of industry, be it in education, healthcare, software development, consultancy, and so forth. We have also learned that the first step to Lean is to identify all value-adding and non-value-adding activities. Your next step is to eliminate the wasteful activities.
By doing so, Lean allows you to cut waste and maximize the efficiency of your resources by focusing on only value-adding activities. In the simplest terms, Lean helps you cut the fat from your processes so you can focus on what matters. However, your work does not stop there. Lean invites you to apply those principles permanently and everywhere in your organization. This is called continuous process improvement which paves the way to operational excellence.
This brings us to our “How to See Waste” Series – Lean Office edition. With it, we want to open your eyes and help you see the individual as well as universal types of waste in an office environment. By doing so, we hope both businesses and individuals understand the importance of Lean thinking and can apply those principles in the office and beyond.
In the first post of the series, I introduced the eight types of waste which are as follows:
- Defects
- Overproduction
- Waiting
- Non-utilized Talent
- Transportation
- Inventory Excess
- Motion Excess
- Extra-processing
Lean Office: How the Muda of Waiting Looks Like in an Office
How often do you find yourself unable to finish a task because you are waiting for a customer to respond to an email, or you were flooded with ineffective meetings requests or waiting for the computer to load a program, or for your manager to finally review and approve your budget?
In the office, the Muda of Waiting is the interrupted flow of information due to a delay in sharing information or interacting with internal or external stakeholders. Waiting waste means employees are sitting idly unable to continue with a task because they are waiting for a document to be processed and made available. This can be any work received from upstream processes such as information, signatures, or approvals. Waiting waste happens everyday in the office and business systems, causing loss of resources, lower customer satisfaction, and frustration among employees.
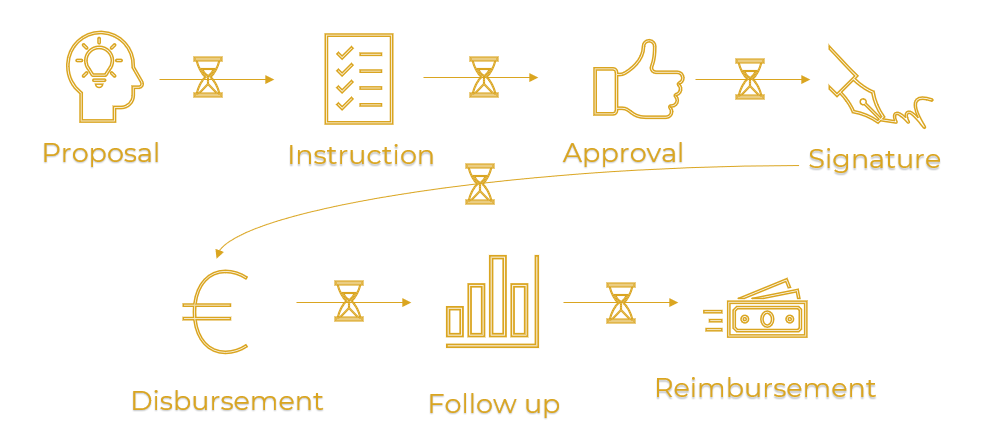
How can waiting cost money? An idle employee will still need to be paid for their time spent at the office. That means you are paying for both value-adding and non-value-adding activities performed by this employee. Your customer will not pay for the time wasted nor will your employees. Idle employees often must make up for their idle time by working overtime, leading you to pay premium dollar on the hour.
The Muda of Waiting in the office can take (but is not limited to) any of the following forms:
- Employees waiting for approvals or signatures
- Waiting for information from the customer
- Waiting for clarification or correction of work received from upper management
- Slow system response time
- Slow computer speed
- Unplanned Downtime (computer, fax, phone…)
- Frequent technology delays/malfunctions
- Bottlenecks and unbalanced workloads
- Attendees late or not present for meetings, scheduling conflicts
- Understaffing
- Employees leaving unexpectedly
- Project budget changes and delays
How to Eliminate the Muda of Waiting
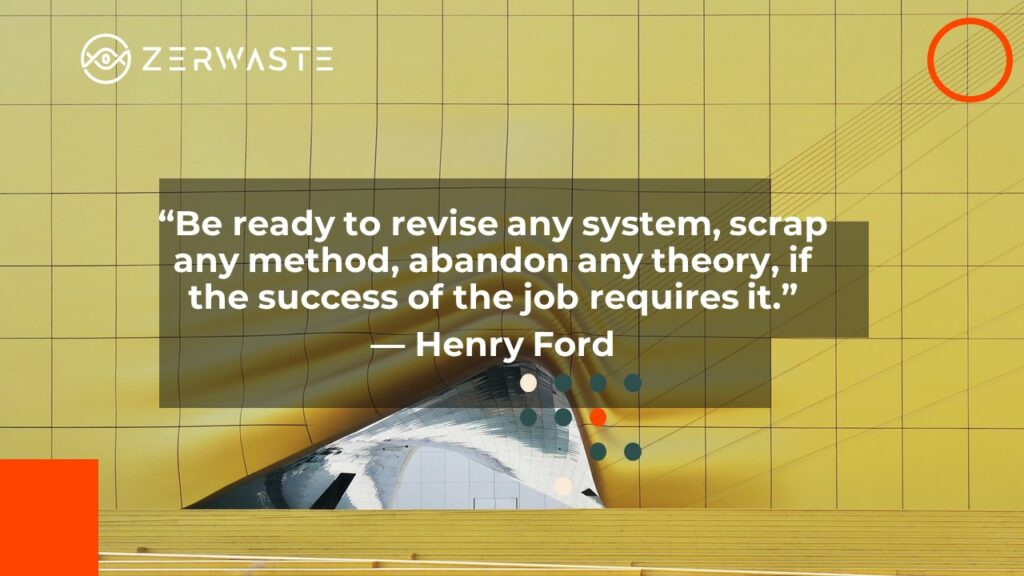
In the office, Waiting Waste is primarily a communication problem. This can be ineffective interdepartmental communication or inefficient management structures that require too many individuals’ inputs. To eliminate the Muda of waiting, the first step is to ask: “How can we reduce approval, communication, waiting, and processing times?”
To systematically remove this type of waste from your office, a plethora of solutions or countermeasures can be implemented such as the standardization of instructions, training, and processes; planning and scheduling solutions for optimal synchronization between departments; reviewing and standardizing required signatures to eliminate unnecessary ones; maintenance, update and/or upgrade your systems to be compatible with current trends.
One way to standardize communication processes is to use deploying CRM and ERP software to streamline the internal flow of data and improve interdepartmental as well as external communication. Evening your internal processes using Lean tools leads to more synchronized processes, interdepartmental synergy, even distribution of workload, clear continuous workflow, and consistent cycle times. Eliminating waste resulting from the Muda of Waiting will have an immediate positive impact on the productivity of your employees as well as your costs. Moreover, reducing waste from overproduction and defects can contribute to reducing Waiting Waste because there is less queueing, and the workflow is not interrupted to make corrections.
However, the main step is to spread the principles of Lean thinking in your office. This means educating your employees on healthy processes as well as helping them see waste in the way they do things. To do that, you must develop multi-skilled flexible human resources who can quickly respond to changing work demands or can be re-tasked to other processes as change happens. Moreover, make sure that the workload is distributed fairly between team members to guarantee optimal performance from each member. Another important aspect of cross-training your employees is that will allow the work to continue even when someone is unexpectedly out.