This article is Part 3 of the “How to See Waste: the 7+1 Muda – Office edition” on the Zerwaste blog. In this post, I will explore the second of the eight wastes of Lean: Muda of Overproduction.
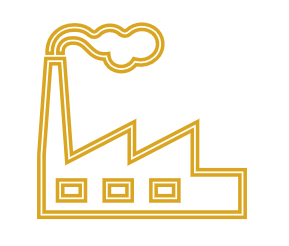
Welcome back to my Lean Six Sigma Journey! In the past weeks, I have introduced the concept of Lean and explored its origins in the manufacturing field building on Henry Ford’s innovative approach to revolutionizing production processes and Japan’s Taiichi Ohno with Toyota Production System (TPS).
So far, we have learned that Lean is a transmittable, transmutable concept that can be abstracted and applied to every aspect of a business regardless of industry, be it in education, healthcare, software development, consultancy, and so forth. We have also learned that the first step to Lean is to identify all value-adding and non-value-adding activities. Your next step is to eliminate the wasteful activities.
By doing so, Lean allows you to cut waste and maximize the efficiency of your resources by focusing on only value-adding activities. In the simplest terms, Lean helps you cut the fat from your processes so you can focus on what matters. However, your work does not stop there. Lean invites you to apply those principles permanently and everywhere in your organization. This is called continuous process improvement which paves the way to operational excellence.
This brings us to our “How to See Waste” Series – Lean Office edition. With it, we want to open your eyes and help you see the individual as well as universal types of waste in an office environment. By doing so, we hope both businesses and individuals understand the importance of Lean thinking and can apply those principles in the office and beyond.
In my previous post, I introduced the eight types of waste which are as follows:
- Defects
- Overproduction
- Waiting
- Non-utilized Talent
- Transportation
- Inventory Excess
- Motion Excess
- Extra-processing
Lean Office: How the Muda of Overproduction Looks Like in an Office
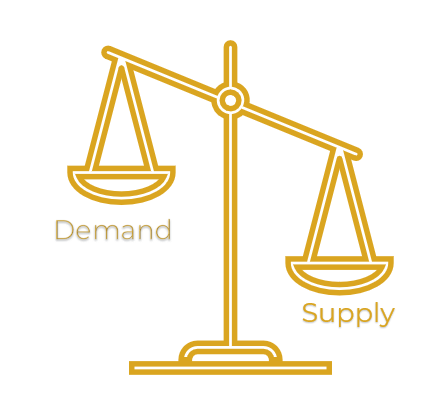
Producing too much of any product or service can negatively impact your business and sacrifice your efficiency. Whether it is developing too many features for your product launch, printing too many copies of your newest report, or CC’ing too many people in your email; overproduction means spending effort before it is needed. That means you are dedicating time, effort, money, and resources that could be better utilized or deployed in other value-adding activities that could help you better develop your product. This can also lead to more waste by increasing the amount of work in progress.
Let us talk about emails and email waste, for instance. Email correspondence is one of the most crucial influential sources of information. However, when not used for its intended purposes, it can lead to significant monetary loss making it one of the main sources of office waste. Today, approximately 333.2 billion emails are sent per day, according to Earthweb. Eighty-five percent of these emails are spam. The average office employee checks their email every 15-30 minutes. The total emails received by that employee in a day are between 100 and 120 out of which they read only 25%. Using a calculator, the average time spent reading emails is between 1 hour and 20 minutes to 2 hours every day.
Two special and powerful features in business email are Carbon copy (CC) and blind carbon copy (BCC). These two functions are two of the most used features in electronic correspondence. Copying people in emails helps you communicate a message with a wide group. However, many of us find ourselves in endless chains of emails without even being the intended recipient. Mismanagement of CC and BCC lines and adding people unnecessarily can translate in serious office waste costing staff members their valuable time which can be used on fulfilling other more pressing tasks. We can extend the concept of Overproduction into everything we do in the office from meetings, reports, presentations, and many others.
The Muda of Overproduction in the office can take (but are not limited to) any of the following forms:
- Any extra or redundant work
- Printing extra copies
- Printing documents (that might change) before needed
- Processing orders (that might change) before needed
- Redundancies in reports and filing systems
- Extra rows in an excel sheet
- Features that were not requested by your client
- Unneeded reports
- Unneeded primary research
- Emails to people that do not need to be cc’d
- Hiring more people than needed
- Printing business card
How to Eliminate the Muda of Overproduction
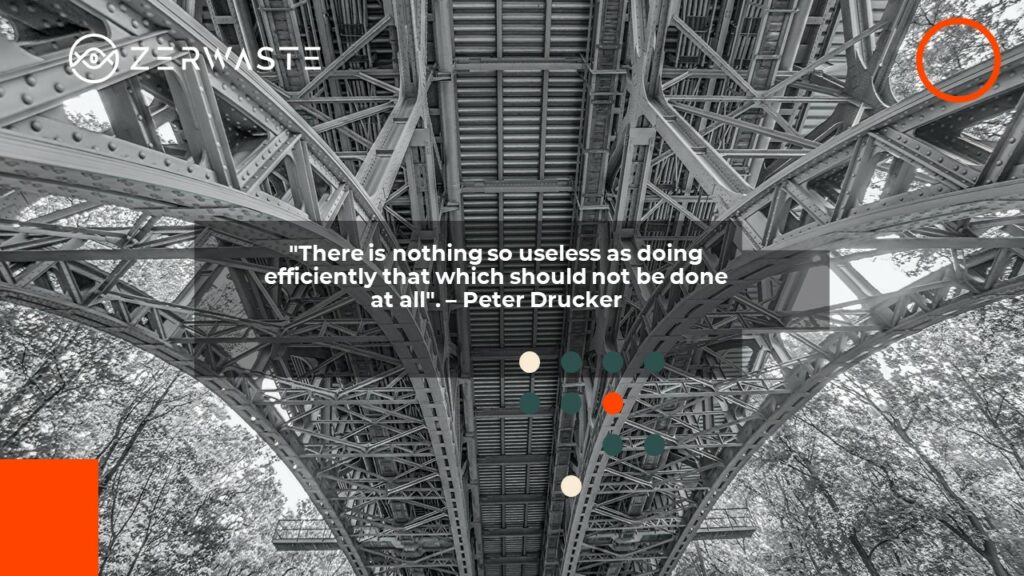
Overproduction in the office is the result of unreliable processes, unstable schedules, inaccurate forecasts, unclear client requirements, poor or no automation, and miscommunication. One way to eliminate overproduction in the office is to be Lean and apply Lean principles. A good rule to follow is to ask: is this much needed at this time?
One of the main concepts of lean is Toyota’s Just-in-Time (JIT) production which means producing exactly your customer needs at exactly the right time. In Lean Manufacturing, JIT is a management strategy that aims to reduce wait time between steps in a process. Applied to an office setting, Just-in-Time means instead of anticipating client or market demand, you wait until your client expresses the need for your product or service and only then produce it. This means dedicating just the right number of resources to complete each activity or process efficiently within time and customer requirements.
In a previous post, I spoke about how Lean is a business principle, mindset, and philosophy that aims at increasing customer satisfaction and creating products that meet clients’ demands while improving business efficiency. Lean asks you to synchronize with your clients and their needs as well as synchronizing with the wider market and current developing trends and processes.
Moreover, Lean asks you to synchronize internally. This means that each department is not an isolated silo but well-integrated, well-synchronized cells. By understanding what each department or individual is doing, you can eliminate redundant work and consequently eliminate overproduction. Another helpful tip is to plan ahead and plan strategically- this means defining the scope of work of each project or process.