This article is part 2 of the “How to See Waste: the 7+1 Muda – Manufacturing edition” on the Zerwaste blog. In this post, we will explore the first of the eight wastes of Lean: Defects.
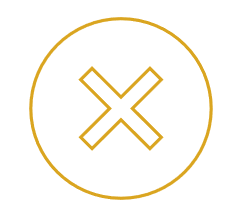
Welcome back to the Lean Six Sigma Journey. Previously, we had presented the concepts of Lean wastes within the Lean Office approach. We have learned that Lean is a transmittable, transmutable concept that can be abstracted and applied to every aspect of a business regardless of industry, be it in education, healthcare, software development, consultancy, and so forth.
We have also learned that the first step to Lean is to identify all value-adding and non-value-adding activities. The next step is to eliminate the wasteful activities.
By doing so, Lean allows you to cut waste and maximize the efficiency of your resources by focusing on only value-adding activities. In the simplest terms, Lean helps you cut the fat from your processes so you can focus on what matters. However, your work doesn’t stop there. Lean invites you to apply those principles on a permanent basis and everywhere in your organization. This is called continuous process improvement which paves the way to operational excellence.
This brings us to our “How to See Waste” Series – Lean Manufacturing edition. With it, we want to open your eyes and help you see the individual as well as universal types of waste in a Manufacturing environment. By doing so, we hope both businesses and individuals understand the importance of Lean thinking and are able to apply those principles in the office and beyond.
In my previous post, I introduced the 8 types of waste which are as follows:
- Defects
- Overproduction
- Waiting
- Non-utilized Talent
- Transportation
- Inventory Excess
- Motion Excess
- Extra-processing
Lean Manufacturing : how the Muda Defects look like in a manufacturing
DOWNTIME: Defects
Defects in manufacturing are a particularly good example of how flawed processes can result in waste. They are products that have been manufactured with errors and that do not meet factory specifications or customer requirements. They constitute the number one cause of value loss in lean manufacturing and are the most obvious form of waste to eliminate when applying Lean principles. Defective products are an expensive form of waste that can overspill into other forms of waste such as transportation, overproduction, or overprocessing.
We can take some examples of defects in Lean Manufacting:
- Large variance in inventory
- Lack of proper quality control throughout the process workflow
- Scraping production
- Parts assembled with the incorrect plan
- Parts damaged due to excessive handling
- Faulty parts that have reached the customer
- ,…
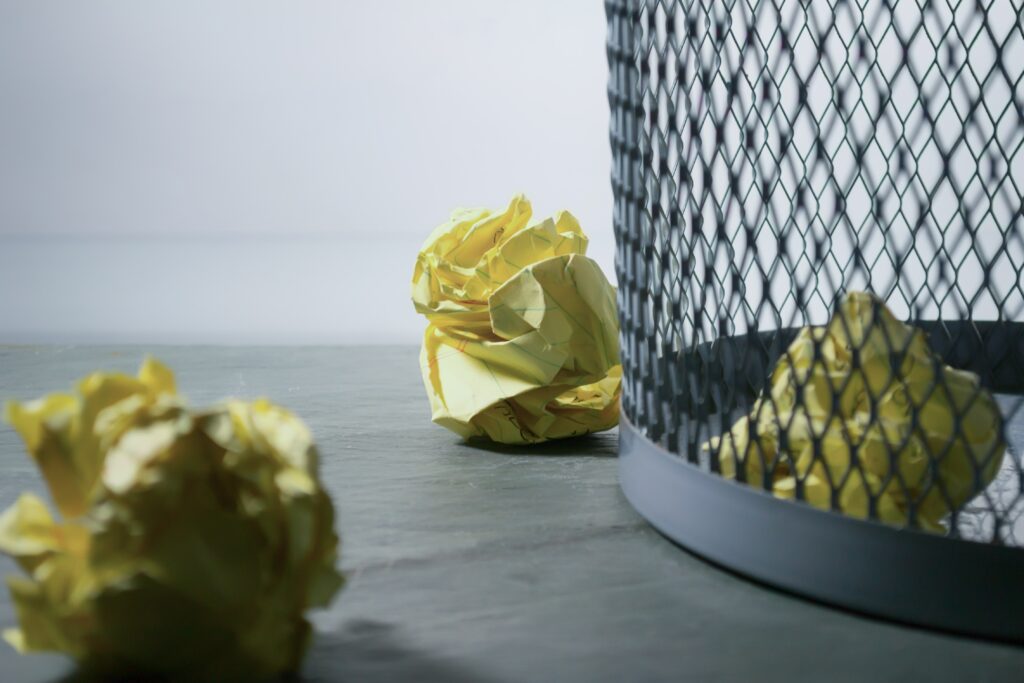
How to eliminate the Defects
They are different ways to eliminate the Muda of Defects. As described above, the defects could be due to manufactured with errors and do not meet factory specifications or customer requirements. The first way to eliminate this waste is taking account of these issues to tackle these errors.
We can take an example of a Lean Management tool: using the Plan-Do-Check-Act (PDCA), also known as Deming Cycle, to reduce defects. This cycle is a philosophy of continuous improvement focusing on the continuous learning and the knowledge creation. After doing all the cycle, defects analysed should not appear more or should show a decrease trend in its appearance. The PDCA cycle is a tool that facilitates the detection of improvement opportunities, as well as the development and implementation of the same Lean Manufacturing projects.