More and more companies are asking how to integrate circular economy in their processes and at Zerwaste, we are convinced that Lean Manufacturing and Value Stream Mapping could be of great help to start this journey. This article aims to demonstrate how the lean tool, Value Stream Mapping can be used to identify and reduce losses increasing value creation from the circular economy point of view.
But first, let’s focus on building a common understanding of those concepts.
On the one hand, Circular Economy is offering to close the loop in the production of goods and services. The objective is to reduce the depletion of natural resources, pollution, and high levels of production. According to the Ellen MacArthur Foundation (2013), it is possible through:
- The rethinking and redesigning of products and services
- The implementation of recirculation of materials,
- The generation of natural systems,
- And the reduction of pollution and waste generation.
On the other hand, Lean Manufacturing is a philosophy that focuses on the development of productivity through the elimination of waste and the increase of value obtaining more efficient systems (Nadeem et al., 2019).
In the literature, it was observed that Circular Economy (CE) and Lean Manufacturing have been previously combined for the elaboration of conceptual frameworks at a strategic level (Nadeem et al., 2019). As you can see, they have in common the terms of waste and value, even if they have different meanings of value and waste. However these meanings could complement each other and bring benefits to the development of the manufacturing sector.
Finally, the Value Stream Mapping (VSM) is a lean management tool that helps visualise the steps needed to take from creating a product to delivering it to the end customer (cradle to gate). Nowadays, the VSM can include some sustainable and environmental aspects, key to the circular economy and could therefore be used to represent, evaluate and improve a circular production system. Another key element to transform a VSM in a VSMc (circular VSM) is to close the loop of the process, by mapping value of a product as it is: used, maintained, reused, remanufactured, recycled, incinerated, or used for landfill. A VSM establishes the evaluation criteria for circular systems, considering the concepts of value and waste, similarly to a life cycle assessment. In the study of Sustainable VSM by Faulkner and Badurdeen (2014), four dimensions are taken into account in the VSMc:
- Economic: represented by the time taken by the product from its arrival to the production process until it is delivered to the final customer.
- Environmental: represented by the water required and used, the net loss, and energy (transport, process) consumption.
- Social: quantified through the indexes of physical work ( ranging from 0 to 56 measured by answers from a questionnaire) and work environment (measures on a scale of 0-5; to cover 4 risk types: electrical systems, hazardous chemicals/materials used, pressurised systems and high-speed components).
- Circular: measured by the respective measure of circularity and longevity.
These 4 dimensions are necessary to the evaluation of circular systems and are evaluated through the VSMc. Adding all these dimensions in a standard VSM tool proves that a circular system can be represented and evaluated by the VSM using the same methodology:
- Identification of improvement points
- Appropriate solution to generate a new VSM
- Comparison of current and proposed situation to obtain significant improvements in the four dimensions of circular performance.
An application of VSM to improve circular systems has been demonstrated by the University of Grenoble in 2021[1]. The proposition to represent a circular supply chain through the VSM has considered an application for end-of-life products restored to “like-new” conditions” (Turki et al., 2017), including two possibilities:
- Remanufacturing: process involving a transformation of the product to be integrated into the linear supply chain (linear process) to obtain new products
- Refurbishment: reconditioning process that is carried out completely parallel to the linear supply chain.
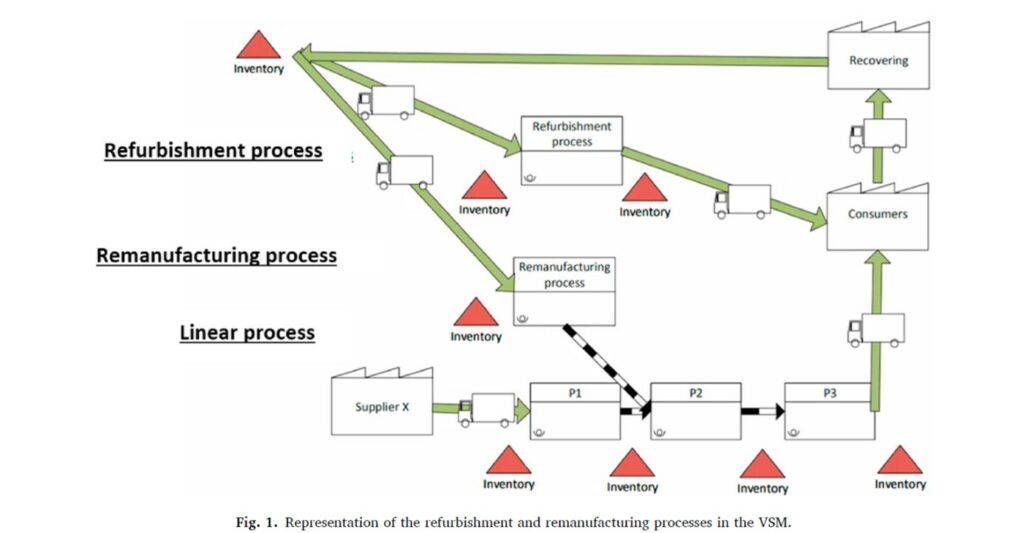
In conclusion, thanks to existing lean tools, circular systems can be:
- Represented in the updated VSM (VSMc)
- Evaluated via specific metrics (economic, social, environmental, and circular), using the (shared) concepts of value and waste.
- Analysed to detect waste and improvement opportunities
- Improved through correction roadmaps and proposals to reduce losses
- Spotlighted as value creation processes thanks to monitoring and reporting
That’s why, it is relevant to create a link between circular economy and lean management (lean circularity) as it offers a clearer vision and it could help decision makers to obtain relevant information to support the decisions from an operational perspective.
[1] Maria Victoria Hernandez Marquina, Peggy Zwolinski, Fabien Mangione (2021), Cleaner Engineering and Technology, Application of Value Stream Mapping tool to improve circular systems, University of Grenoble Alpes, CNRS, Laboratory G-SCOP, 38000, Grenoble, France.
Circularity Gap Report 2022: Time for a circular economy
More value from fewer resources: how to expand value stream mapping with ideas from the circular economy, C. Hedlund & P. Stenmark, E. Noaksson, J. Lilja, Mid Sweden University, May 2020.
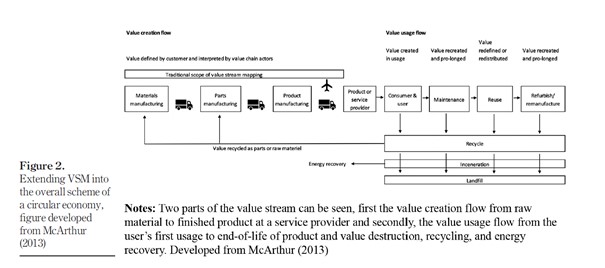
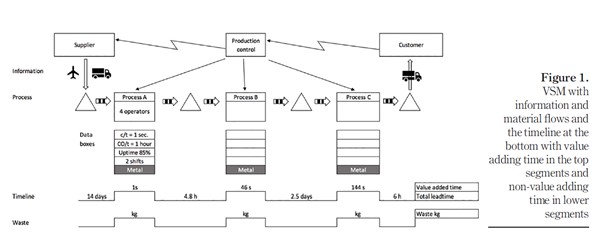